製品開発ポイント-品質管理に重要なデータ分析
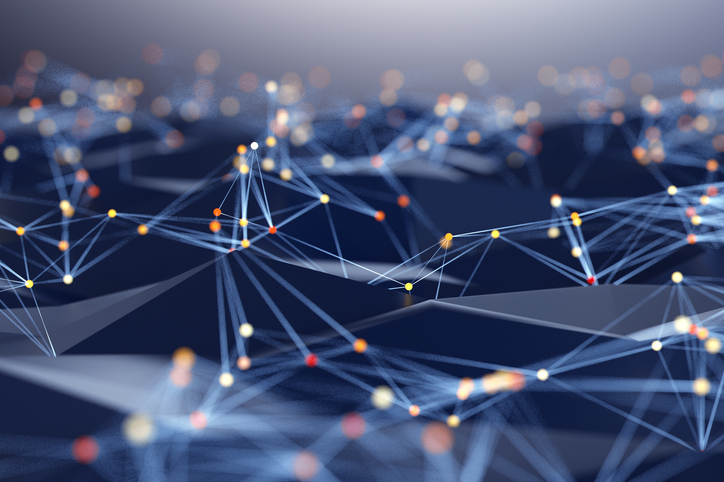
品質を管理すること、そしてそのデータを分析する必要性についてご説明します。
1.品質を管理する
量産において品質を管理することは量産活動の根幹であって、品質が管理されていない量産とは「偶発的な製造の連続」ということになります。ある意味で「量産」ではないといえます。
そこで、品質管理を行うにあたり2つの側面があると言えます。
一つは、連続される製造工程においての品質の安定具合を監視すること。
二つに、品質を安定化改善するための測定です。
2.品質の工程能力
一つ目の「連続される製造工程においての品質の監視」とは、どのような品質で製造が繰り返されているかを測定することであり、この製造品質の安定具合を「品質における工程能力」と呼びます。工程能力が完全に品質安定レベルであれば、もはや出荷検査は不要でしょう。不良が製造されない工程であると言います。
全くバラツキの無い製造工程というのはあり得ず、必ずバラツキは生じます。あるバラツキを現象レベルごとの発生頻度で集計した時に、その平均値からのズレを偏差といい、その分布から標準偏差という品質の工程能力目標値を導き出す現状の工程バラツキ状態が認識できます。
その上で、良品として認められる品質領域にバラツキをどの程度収めることができるかをセンター値からの波形距離で分割し、「σ」シグマで表します。(例えばセンターから±3σで規格外バラツキは1000分の1.4。4σになると100,000分の3.2となる。6σで1,000,000,000分2)
計算は少々面倒ですが、このように3σより4σ・5σへと工程品質を安定化させれば、不良発生率は低下し、品質管理上良化された製造と言えます。
この工程のバラツキ状態を常に監視するためのデータを収集し分析することが工程管理となります。
3.QC7つ道具
発生する不良事象(品質バラツキの中で不良となる領域)をどのように改善するのかを検討するため、データ収集し分析することを「品質改善にためのデータ分析」と呼びます。
これは、工程のバラツキを掌握することを主目的とするのではなく、「顕在化した不良の改善」や「製造工程における不良率の改善」を目的とした分析のためのデータ収集なのです。勿論、工程バラツキを監視することで安定維持ラインが認識できるので、工程の異常バラツキは発生しないのです。
要するに突発的な不具合発生や予測外の不良事象発生の際に、その原因分析を目的にしたデータ収集と分析を指すとイメージして頂ければと思います。
具体的は「パレート図」「ヒストグラム」「管理図」「散布図」「特定要因図」「チェックシート」「グラフ」という7種の手法を活用する分析手法が推奨されており、それぞれ、不良現象を品質特性として捉えて、不良原因や不具合要素を顕在化・可視化できるように分析する手法です。それをもとに改善アプローチのポイントとして活用するものです。
品質管理の手法としては昔からあるので、それぞれの手法について様々な手引書もあります。上手に活用し品質管理に役立てたいですね。