製品開発ポイント-「歩留まり」について
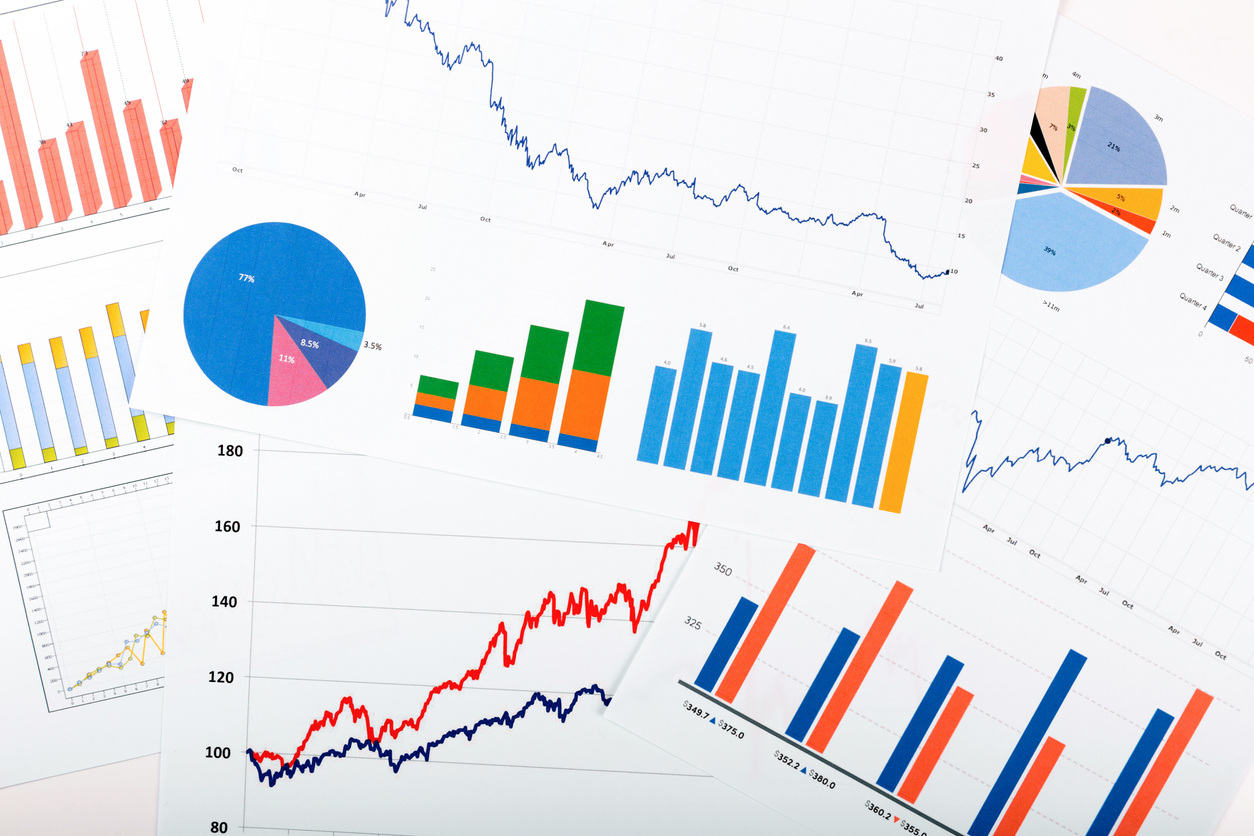
モノを作るための材料量と発注計算。その歩留まりについて説明します。
1.歩留まり率を考慮するとは??
先述のコップで考えてみましょう。コップは100gのプラスチック製品であるなら、たしかに100gのプラスチック材料が1個の材料量です。しかし現実には、この100gのコップを製造する過程で一定の率でロスが発生するため実際に製造できるコップの数は100個を下回ってしまいます。
この投入材料から製品を作れる有効度を「歩留まり」と表現します。
そして、製造に際し投入された材料量に対して何%の材料が実際のコップとして活用されたのかを「歩留まり率」として表します。10Kgのプラスチック材料を投入して90個のコップが製造できたのなら「歩留まり率90%」となります。(100g×90個)/10,000g=90%となります。歩留まり率は高いほど有効的に材料が利用されていることになります。
したがって、歩留まり率は直接製造原価に大きく影響するのです。
2.歩留まり率を下げる要因のロスとは?
では、なぜそのようなロスが発生するのでしょうか?
ほとんどの製造において、製造される製品品質等をみて製造機械の設定を調整するという製造準備の前作業があります。この時も製造しながら調整するため材料は使用されています。また、指定数量を製造し終えた時にもある程度の材料が残ります。これらで消化される材料がロス材料になります。
カレーを作るときに、ニンジンやジャガイモの皮を剥きます。ニンジンはヘタの部分は切り落とします。ジャガイモも芽の部分を削ぎ落します。
ロス材は廃棄になるものですので、これらは調理食材におけるロス材ということになります。
3.不良も歩留まり率を下げる要因
生産された製品の中から検査の結果で不良品が検出されたとすると、最終的な良品数が生産数量となります。そのため、不良の発生も歩留まり率を下げる要因となります。
製造上のロスと不良数を差し引いたものが製品となりますので、「良品率+ロス率+不良率=1」ということになりますから、歩留まり率とは「100-ロス率%数-不良率%数=歩留まり率%数」となります。
歩留まり率は材料の特性でも変化しますし、また製造方法や製造技術の影響でも変化します。
【歩留まり率の向上のための工夫】
より良い材料を選定することで、同じ量の材料でも多くの製品を製造することができれば「歩留まり率が高い」製造になります。また、製造技術の工夫で製造準備作業を軽減することができれば、その分ロス材を減らすことができます。これも歩留まり率を向上することに貢献します。
このように、「ロス」と「不良対策」というポイントに工夫と改善を図ることは歩留まり率を向上させる直道になります。
それとは別な視点で歩留まり率向上を考えることもできます。例えば、キャベツの芯やダイコンの葉のように廃棄してしまう部分を調理して別なメニューに利用することで「食材における歩留まり率の向上」となります。要するに、「廃棄」にするのではなく「利用価値」を見出す。これも全体としての歩留まり率の向上につながるのです。キズがついた製品や食材を「B級品」として安価で販売することも歩留まり率の向上になっているのです。
ちょっとしたアイデアが歩留まり率向上つながる場合もあります。
歩留まりについて「考える」ということが向上への大切なポイントとなります。